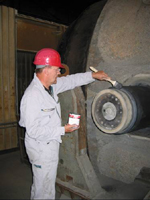
OKS 111/OKS 230 |
The lubrication of bearings of foundry ladles in metal plants mostly takes place with a copper paste. According to this one has to relubricate very often. This only is possible when the foundry ladle is cold. When the lubrication fails, the foundry ladle does not return automatically into the required position and has to be arranged by hand. Intention of a inquiry of a german metal plant was, to encrease the operation safety and the relubrication periods according the operation time of the foundry ladle. A foundry ladle is about 20 days in operation. In this time it is filled about 90 times. The measurement of the temperature of the bearing work performed temperatures cleary lower than supposed. The joints of the foundry ladle were cleaned with OKS 2611. Afterwards the bolt was coated
with OKS 111. The operation lubrication takes place with OKS 230. The demand is about 1,5 t paste a year. |
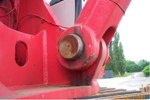
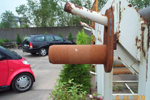
OKS 250 |
A big german manufacturer of diggers had real problems with tribo-corrosion at the bolts. Therefore an non-destructive removal of the bolts was not possible any more. With OKS 250 the tribo-corrosion is reduced to a minimum. The removal of the bolts is even after a long operating time possible without any problem.
|
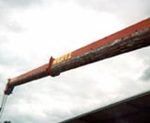
OKS 277 |
Telescopic extension arm cranes are more and more used. Their fast disposability in combination with the minor work for the handling make them a economic alternative to normal cranes. Encreasing limite loads and bigger range open up new application fields. A smooth operation is one of the most important requirements for an economic operation. But most of the so far used greases were not suitable for high loads and extrem wide ranges. By the extension of the crane arm stick-slip affect appeared and the load could come in dangerous vibrations. The drivers of these crane even had a more terrestrial problem. When raining, the grease dropped onto the windscreen. To continue (mostly when still raining), the cleaning of the windscreen has to be nessasarry. The relubrication intervall of OS 277 is eight times langer than with
the so far used grease. And even with high loads and with wide ranges no stick-slip effects appeared. Also the problems with the windscreens are solved, too.
|
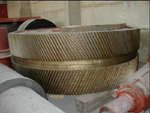
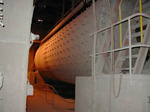
OKS 30 |
n a ball mill for the generation of the raw material for the cement clinker production a duo-planetray gear with 2 x 1200 kW is in use. This gear is deposed to extrem forces, mainly vibrations and impacts. This leads to extreme wear at the gear toothes and therefore to untimely break down of the gear. Through the addition of 3 % of OKS 30 (for 5,500 l this is about 200 l OKS 30) the vibrations of the gear could be vertifiable reduced as well as wear and friction. |
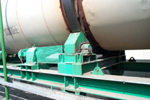
OKS 335 |
In a tar mixing plant the lubrication of the bearings at the rotary kiln oven is successfully done with OKS 335. Main items for this application were the very good pressure properties and the application through automatic sprayer |
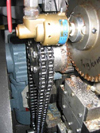
OKS 336 |
The drive of the rolls in a backing station takes place through chains. Onto this so far oil lubricated chain rests of pasty dropped down and adhered. The chain is highly stressed. The intention was to prevent the adherend of the pasty and to encrease the relubrication interval. With OKS 336, a dry chain lubricant for the food industry, both intentions could be reached.
|
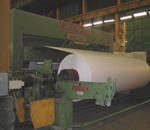

OKS 352 |
In a hungarian papermill the floor conveyor chain for the transport of the paper rolls are lubricated with OKS 352. These very long chains are affected with very high traction forces. In addition paper dust accumulates on the chain and closes the chain links so that the lubricant can‘t penetration into the chain link. OKS 352 with it‘s very good wear protection properties and it‘s high cleaning properties work performed a clearly reduction of wear and a extention ofthe relubrication intervals |
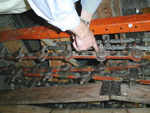
OKS 352 |
Conveyor-chains of paint shops are deposed to temperatures of about 180 to 220 °C. The dust of the paint evaluates on the chain and closed the chain links so that the lubricant can‘t penetrate inside the chain link. OKS 352 fulfilles the requirements concerning wear protection, temperature stability and cleaning properties.
|
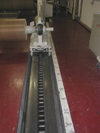
OKS 352 |
At a manufacturer of non-woven materials the calender rools are strained by chains. This chain is highly stressed and the dust of the non-woven material accumulates on the chain.OKS 352 fullfills the requirements concering cleaning properties and wear protection.
|
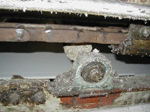
OKS 352 |
At a big manufacturer of plasterboards OKS 352 is used for the lubrication of the conveyor-chains through a 12 chamber drying oven. Inside the oven the chain is warmed up to 200 °C. Beside the good temperature stability of OKS 352 the cleaning properties and the wear protection were deciding for the application in comparision to several competitors. The demand for one line is about 1,000 – 1,500 l a year.
|
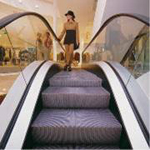
OKS 353 |
KS 353 , for the lubrication of escalators.
|
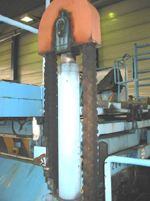
OKS 3541 |
The chains of the lifts of freight containers on airports are completly deposed to the weather. In addition, these chains are extremely high stressed. First trials with OKS 451 failed in comparision to the so far used lubricant. After one week, corrosion appeared again. Also the reduction of wear was not in the way the customer expected. OKS 3541 adduced the desired result of wear and corrosion protection.
|
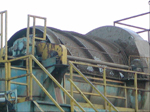
OKS 403 |
The sugar-beets for the production of sugar are washed with enormuos drums. The roller bearings of this draum were lubricated with a regular multi purpose grease. Through the extreme influence of water there were often problems with the breakdown of the bearings. OKS 403 is absolutly resistant to water and warrants therefore the nessesary operation safety for the seasonal operation. The demand für one season is about 600 kg.
|
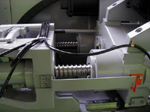
OKS 404 |
At pressure casting machines the ejectors are moved by a screw ball. OKS 404 is superior to the so far used multi purpose grease because of it‘s extremely stable thickener. The relubrication intervals could be clearly extended.
|
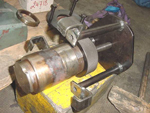
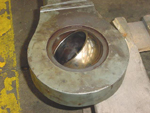
OKS 410 |
At the guiding support of the wheel chassiv of railway trains OKS 410 is successfully applicated for the lubrication of the ball joint |
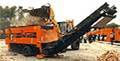
OKS 410 |
Mobile roll shredder are used to reduce the volume of waste sites. All the different matials are crushed. The extreme stress of the bearings in combination with slow rotation demands very high requirements to the lubricant. Intension of our customer was a clearly extrension of the relubrication intervals in comparison to the multi purpose grease used before. The amount of this grease was at about 20 kg a day for one machine. With OKS 410 the relubrication intervals and the operation safety could be extended. |
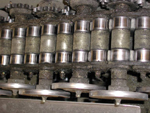
OKS 422 |
At an hungarien manufacturer of fluorescent tubes the conveyor chain for cutting the glas tubes was lubricated with a regular grease. The temperature of this chain is about 140 °C. This conveyor-chain is made of hundreds of needle bearings and had to be lubricated every day by hand. With OKS 422 the relubrication interval could be extended up to eight weeks |
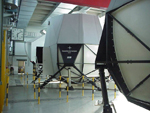 OKS 422 |
At flight simulatores the movements are generated by ballscrews. OKS 422 with it‘s thin synthetic base oil and it‘s extreme stable thickener contributes that the movements of the ballscrews are senitive transfered. |
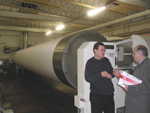 OKS 4220 |
At calender rolls in the papermanufacturing industry through the bearing, diameter of the bearing is about 45 cm, the pipe with the thermal oil for heating the rolls gets through. The roll is about 8 m long and has a weight of about 15 tons. The thermal oil is heated, depending of the requirements, up to 300 °C. This temperature devolves onto the bearing. The high temperature grease used before dropped out of the bearings. This cause two times a year a fife days shut down and the exchange of the bearings. With OKS 4220 the relubrication interval encreases up to 1 year. In addition the operation reliability clearly encreased, too.The demand of one roll is 5 kg. |
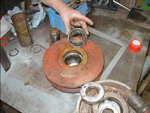 OKS 4220 |
A german manufacturer of rooftiles lubricated the bearings of the transport wagons with a normal high temperature grease. Therefore the bearings had to be exchanged every month, they looked for a better lubrication. Inside the tunnel there is a temperature of about 200 °C. Although the customer declined OKS 4220 out of the high price, the bearing of one wagon were lubricated for testing with OKS 4220. For more than one year this wagon runs without anyproblem. Meanwhile, all wagons are equipped with OKS 4220. The failure of regular fully synthetic greases is not caused by the temperature. The slow movements of the bearings and the long time inside the oven are the main points for choise of the lubricant. Under these conditions only a grease with solid lubricants can stand
on. |
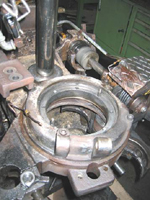 OKS 424 |
For general lubrication duties in the glas industry a regular multi purpose grease is because of the high temperatures not sufficient. OKS 424 sets up adequate reserves. |
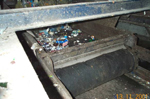 OKS 450 |
At a potential recyclable process company OKS 450 is used for the lubrication of the conveyor-chains. Intention of the customer was, to increase the relubrication intervall in comparision to the so far used normal chain lubricant. OKS 450 is significant resistant to most of the incidental fluids of waste separation and therefore fullfills a essential point to encrease the relubrication intervals. |
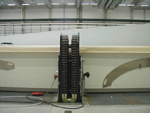 OKS 451 |
The wind energy is one of germans fastes growing industries. A german manufacturer of rotor blades for wind energy plants uses OKS 451 for the lubrication of the chains of the computer controlled locomotor system to move these rotor blades. |
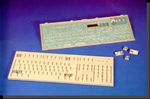 OKS 475 |
uses for the lubrication of the PC-keyboard successful OKS 475. Just in warmer countries the grease used before dropped of the lubricating points onto the electronic parts. This leads to interferences and caused significant reclamations. Beneath the good compatibility of OKS 475 with plastics, the wide temperature range and the easy application were diciding for the use. Beside the extreme lox amount of grease (above 1 g), the demand is about 500 kg a year. |
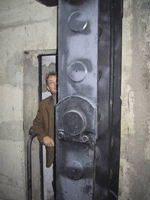 OKS 491 |
At the lifting chains of the floodgates of the Donau-chanel consistenly problems of wear and corrosion appeared. These extremly stressed chains are moved very infrequent and are placed outside. After priming the chain bolts with OKS 511, OKS 491 is used for the operating lubrication of the chain. Also the drive gear grim is lubricated with OKS 495 |
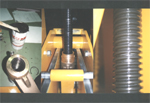 OKS 495 |
The manufacturer of the lifts for the maintenance of the german ICE-trains uses after long and unsuccessful trials OKS 495 for the lubrication of the spindles. Lubricants used before it were shift away and through this, the extremly encreased friction turned the engines off. Also, after a short operating time stick-slip appeared. Each spindle has to lift a weight about 15 t. The relubrication interval is, depending on the operating hours, monthly. |
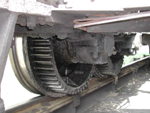 OKS 495 |
In a coking plant of a german steel manufacturer the dirve to move the spinning machine is successfully lubricated with OKS 495. |
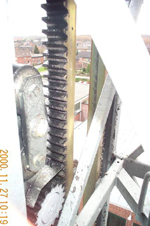 OKS 495 |
In a german mine the gear drive of the winding tower is automatically lubricated with OKS 495. |
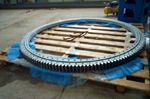 OKS 510 |
In wind energy plants the rotor is sensor controlled alignet to the wind direction. The gear rim to adjust the rotor-head is exposed to extensive stress and aggressive enviromental influences. The relubrication of the gear rim inside the rotor head is very time-consuming. Ambition of our customer therefor was to reach a relubrication intervall of minimum 6 month. Also the service lubricant should be applicated by an automatic module. Critical points of this lubrication were beside the mentioned factors the very high surface pressure on the gear-toothes in combination with sporadic movements and the vibrations transfered from the rotor to the gear grim. |
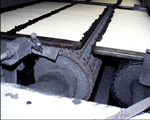 OKS 536 |
For manufacturing backery products OKS 536 is used for the lubrication of conveyor chains running through the backery ofen. |
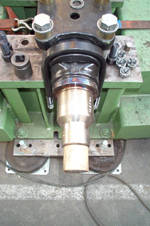 OKS 575 |
A big german manufacturer of truck-axles approached us with a problem of tribo-corrosion at the shaft. Additional intention was to improve the handling. OKS 575 shows lowest friction-values during the assembling of the axle and also has advantages in handling compared to the prior used paste. Also the problem of tribo-corrosion was solved to the customers satisfaction. For maintenance OKS 571 is used. The demand of the initional equipment is about 400 l per year |
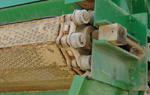 OKS 670 |
The conveyor chains in a german grit plant are lubricated with OKS 670. Main points for this application are the good cleaning properties in combination with the good lubrication properties warrented also under extreme forces through the solid lubricants containd in OKS 670. |
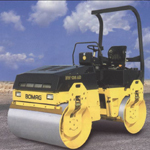 OKS 1000 |
In the initional equipment a german manufacturer of road rollers successful uses OKS 1000 as a damping oil for the striking mechanism. The demand is abbout 10 t per year. |
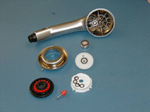 OKS 1110 |
A manufacturer of shower fittings uses for the lubrication of the mechanical parts inside the shower-heads OKS 1110. Beside the absolute resistance to water the good compatibility to plastics and the physioloical harmlessness of OKS 1110 were the determining factores for the application. For a easier assembling, also the sealings are lubricated with OKS 1110. |
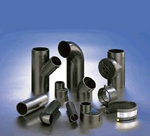 OKS 1110 |
A big german manufacturer of installation systems for the sanitary branche uses OKS 1110 to lubricate the sealings of the tubes. The lubricant is automatically applicated. The demand is about 1.2 t per year. |
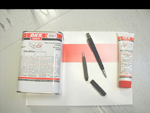 OKS 1300 |
From a german manufacurer of high-quality writing utensils came a request for an appropriate lubrication. The lubrication so far dropped of the writing utensils by and by. For optimal adhesion of the recommended lubricants, the parts are cleaned of production leavings, such as mold release agents, with OKS 2650. The fine thread at the ball-pen peak now is coated with OKS 1300, the mechanical parts inside the writing untensils are lubricated with OKS 1110 |
 OKS 8370 |
Most of the transport chains in saw mills are placed outside. For the lubrication of these chains only a biological degradable chain lubricant is to be considerd. Because in addition to the main requirement of a chain lubrication the polution of the chain with sawdust and other dust is extensive, good cleaning properties of the lubricant is required for a proper lubrication. The requirements concerning enviromental compatibility as well as the requirements of a reliable lubrication are fullfilled by OKS 8370. The demand is about 600 l per year. |
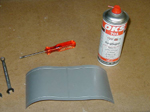 OKS 701
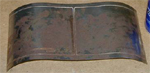 |
Contrary to other statements of the advertisment the corosion protection of competitor products is not very good. In comparision with OKS 701 after a short period of salt water spray test a clear difference is shown. |
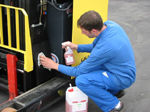 OKS 2650 |
Beside many other cleaning examples, OKS 2650 also is suitable as a cleaning additive for cleaning machines and in high pressure cleaners. |
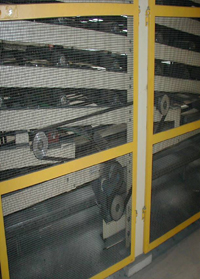 OKS 2901 |
Drive of transport rollers in a storage with v-belts. Encrease of the traction force and extension of the service life through OKS 2901. |